Самые ранние свидетельства использования отжига для размягчения холоднодеформированного металла относятся к концу пятого тысячелетия до нашей эры. Этот отжиг был первым случаем термической обработки металлов. Изготавливая оружие и орудия из железа, полученного методом обжига, кузнец нагревал руду, в древесном угле, для подготовки к горячей обработке (ковке).
Нагревание науглероживаало железо; то есть происходила цементация - форма химической обработки. После охлаждения кованого изделия из науглероженного железа в воде кузнец заметил увеличение твердости и улучшение других свойств. Процесс закалки науглероженного железа закалкой в воде применялся с конца второго до начала первого тысячелетия до нашей эры. В «Одиссее» Гомера (восьмой-седьмой века до нашей эры) мы видим строки: «Когда кузнец окунает светящийся топор или секиру в холодную воду, железо шипит и с бульканьем становится сильнее, закаляется в огне и воде». В пятом веке до нашей эры этруски закаливали зеркала из бронзы с высоким содержанием олова в воде, главным образом для улучшения блеска после полировки. При быстром охлаждении металл становился более твердым и менее хрупким. Цементирование железа в древесном угле или другом органическом веществе с последующей закалкой и отпуском полученной стали стало широко использоваться в средние века для изготовления ножей, мечей, напильников и других инструментов. Не понимая изменений, происходящих в металле, средневековые мастера часто приписывали улучшенные свойства, полученные при термообработке, сверхъестественным причинам.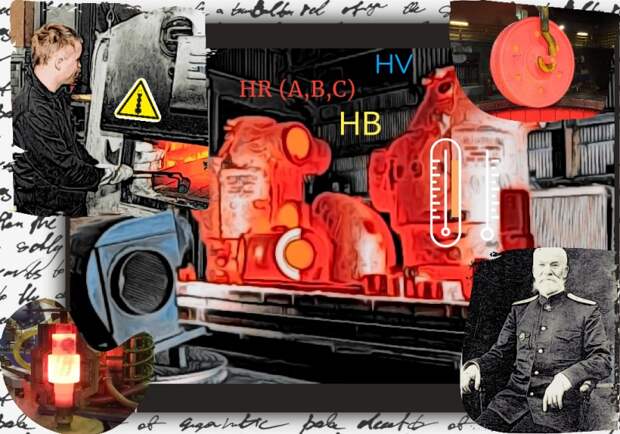
Технологические потребности, особенно необходимость производства стальных орудий, превратили термическую обработку из искусства в науку. В середине XIX века, когда военные стремились заменить бронзовые и чугунные пушки более прочными, стальными аналогами, проблема производства высокопрочных стволов приобрела большую актуальность. Несмотря на то, что металлурги знали процедуры плавки и разливки стали, стволы орудий часто взрывались без видимой причины. На Обуховском заводе в Санкт-Петербурге наблюдая под микроскопом шлифы, приготовленные из дул орудий, и изучая под лупой строение изломов в месте разрыва, Дмитрий Константинович Чернов (1839 — 1921 гг.) пришел к выводу, что сталь тем прочнее, чем мельче ее структура.
В 1868 году Чернов обнаружил внутренние структурные превращения, происходящие в охлажденной стали при определенных температурах, которые он назвал критическими точками a, b, c и позднее в 1878 году была названа точка d. Нагрев металла до определенных температур с использованием процедур термообработки приводит к различным фазам. Фазы - это физически однородные состояния сплава. Фаза имеет точный химический состав - определенное расположение и связь между атомами. Некоторые специальные сплавы могут существовать в нескольких фазах при одной и той же температуре.Точка a, значение которой приблизительно равняется 950 К (676,85 C), – это граница закалки. Дмитрий Константинович доказал, что сталь не будет закаляться, если ее не нагреть до этой температуры, какое бы быстрое охлаждение ни было использовано после. Вещество, которое получалось при достижении 950 К, было названо тетрагональный а -твердый раствор. Другое название этой температурной границы – точка темно-вишневого каления (по оттенку цвета, который приобретает расплавленный материал). Если не нагреть сталь до точки b (около 1420 К), она не поменяет своей структуры. Если сталь нагревается до температуры ниже точки а, она не может быть закалена, сталь необходимо нагреть до температуры выше точки b для получения мелкозернистой структуры. Точка c по Чернову – это точка плавления стали (приблизительно 1300-1500 градусов по Цельсию). Выше этой температуры нагревать сплав не имеет смысла. Чуть позже, чем первые три (в 1878 г.), была открыта и точка d (470К или 196.85 С). Согласно исследованию Дмитрия Чернова, именно до этой температуры необходимо охладить сталь для ее полной закалки.
Железоуглеродистый сплав с содержанием углерода от 0,008% до 2,14% называется сталью. В этом диапазоне существуют различные марки стали, известные как низкоуглеродистая сталь (или мягкая сталь), среднеуглеродистая сталь и высокоуглеродистая сталь.
Когда содержание углерода превышает 2,14%, мы достигаем стадии чугуна. Чугун очень твердый, но его хрупкость сильно ограничивает его области применения.
Элементы из легированной стали, такие как никель, марганец, хром и молибден, влияют на положение этих границ на фазовой диаграмме. Некоторые материалы по своей природе твердые. Например, вольфрам - невероятно твердый металл, который находит применение в качестве легирующего элемента в инструментальных сталях. Границы могут сдвигаться в любом направлении в зависимости от используемого элемента.Открытие Черновым критических точек структурных превращений в стали дало научную основу для выбора цикла термообработки для получения требуемых свойств стальных изделий, его первые исследование послужили основой для последующего удивительного прогресса в области металлургии стали, для которой вторжение научных знаний оказалось поистине революционным.
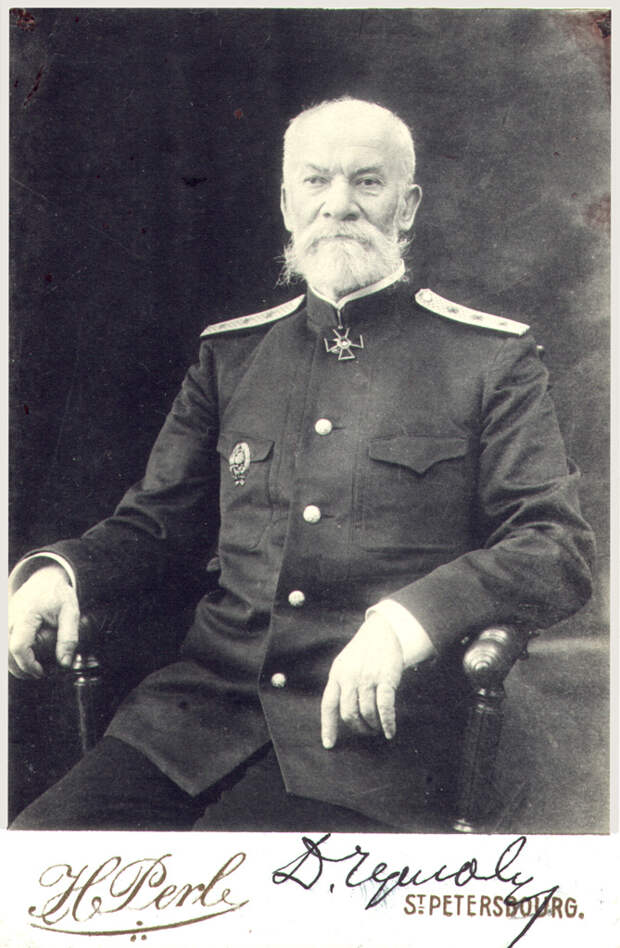
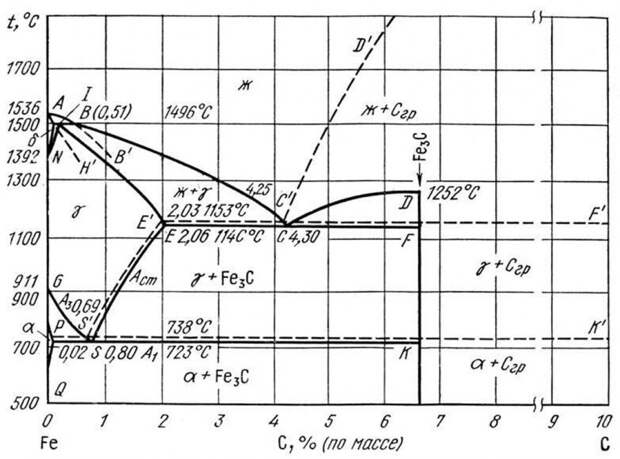
До 19 века знания о термообработке ограничивались набором процедур, накопленных за многовековой опыт. В 1906 г. А. Вильм из Германии открыл дюралюминий и, в процессе этого, упрочнение старением - очень важный метод упрочнения сплавов на основе таких металлов, как алюминий, медь, никель и железо. Термомеханическая обработка медных сплавов, подвергающихся старению, была разработана в 1930-х годах, а в 1950-х годах началась термохимическая обработка стали, что позволило значительно повысить прочность стальных изделий. Современная обработка металлов стала намного более сложной и точной, что позволяет использовать разные методы для разных целей.
Некоторые методы термообработки снимают напряжения, возникшие в более ранних процессах холодной обработки. Другие придают металлам желаемые химические свойства. Выбор идеального метода зависит от типа металла и требуемых свойств.
В некоторых случаях металлическая деталь может пройти несколько процедур термической обработки. Например, некоторые спецсплавы, используемые в авиастроении, могут пройти до шести различных этапов термообработки, чтобы оптимизировать их свойства для применения.
Термическая обработка представляет собой любую из ряда контролируемых операций нагрева и охлаждения металлов, используемых для достижения желаемого изменения их физических и механических свойств, не позволяя им изменять свою форму. Можно сказать, что термическая обработка является методом упрочнения металлов, но также может использоваться для изменения некоторых механических свойств, таких как улучшение механической обработки и т. д. Хотя черные металлы составляют большинство термообработанных материалов, сплавы меди, магния, алюминия, никеля, латуни и титана также могут подвергаться термообработке. Около 80% термически обрабатываемых металлов - это разные марки стали. Черные металлы, которые можно подвергать термической обработке, включают чугун, нержавеющую сталь и различные марки инструментальной стали.
Такие процессы, как закалка, отжиг, нормализация, снятие напряжений, цементирование, азотирование и отпуск, обычно выполняются на черных металлах.
Медь и медные сплавы подвергаются таким методам термической обработки, как отжиг, старение и закалка.
Алюминий подходит для таких методов термообработки, как отжиг, термообработка на твердый раствор, естественное и искусственное старение. Термическая обработка алюминия - это точный процесс. Объем процесса должен быть установлен, и его следует тщательно контролировать на каждом этапе для достижения желаемых характеристик.
Очевидно, не все материалы подходят для термической обработки. Точно так же не обязательно использовать каждый метод для отдельного материала. Поэтому каждый материал нужно изучать отдельно, чтобы добиться желаемого результата. Использование фазовых диаграмм и доступной информации о влиянии вышеупомянутых методов является отправной точкой.
Со временем было разработано множество различных методов. Даже сегодня металлурги постоянно работают над улучшением результатов и рентабельности этих процессов. Это очень важный производственный процесс, который может не только помочь производственному процессу, но и во многих отношениях улучшить продукт, его производительность и характеристики. Рекристаллизационный отжиг холоднокатаной меди снижает предел прочности с 400 до 220 меганьютон на квадратный метр (МН / м2) или с 40 до 22 килограммов-сил на квадратный миллиметр (кгс / мм2), и в то же время увеличивает относительное удлинение от 3 до 50 процентов. Отожженная сталь У8 имеет твердость 180 HB; закалка поднимает показатель до 650 НВ. Сталь 38 ХМЮА после закалки имеет твёрдость 470 HV, а после азотирования твёрдость поверхностного слоя достигает 1200 HV. Предел прочности дуралюмина Д16 после отжига, закалки и естественного старения равен соответственно 200, 300 и 450 Мн/м 2 (20, 30 и 45 кгс/мм 2). Предел упругости σ0.002 бериллиевой бронзы после закалки равен 120 Мн/м 2 (12 кгс/мм 2), а после старения 680 Мн/м 2 (68 кгс/мм 2).
Термическая обработка металлов может быть нескольких видов – термической, термомеханической, а также химико-термической.
- Термическая обработка – воздействие только температур на металл.
- Термомеханическая – воздействие температур и пластических деформаций детали.
- Химико-термическая – наиболее сильный метод, сочетает в себе воздействие температур и химических веществ.
Виды термической и ХТО обработки стали
Отжиг — термическая обработка (термообработка) металла, при которой производится нагревание металла, а затем медленное охлаждение. Эта термообработка (т. е. отжиг) бывает разных видов (вид отжига зависит от температуры нагрева, скорости охлаждения металла).
Закалка — термическая обработка (термообработка) стали, сплавов, основанная на перекристаллизации стали (сплавов) при нагреве до температуры выше критической; после достаточной выдержки при критической температуре для завершения термической обработки следует быстрое охлаждение. Закаленная сталь (сплав) имеет неравновесную структуру, поэтому применим другой вид термообработки — отпуск.
Отпуск — термическая обработка (термообработка) стали, сплавов, проводимая после закалки для уменьшения или снятия остаточных напряжений в стали и сплавах, повышающая вязкость, уменьшающая твердость и хрупкость металла. Отличие отжига и закалки состоит в скорости охлаждения металла после нагрева до критических температур.
Нормализация — термическая обработка (термообработка), схожая с отжигом. Различия этих термообработок (нормализации и отжига) состоит в том, что при нормализации сталь охлаждается на воздухе (при отжиге — в печи).
Криогенная обработка проводится при охлаждении материала до отметок самых низких температур (ниже -153 ° C (-243,4 ° F)). Данный вид термической обработки способствует увеличению твёрдости, износостойкости и прочности металлов в результате трансформации остаточного аустенита в мартенсит. Оборудование для проведения криогенной обработки называется (Криогенный процессор).
В зависимости от насыщающего элемента различают следующие процессы химико-термической обработки:
- однокомпонентные: цементация стали - насыщение углеродом; азотирование - насыщение азотом; алитирование - насыщение алюминием; хромирование - насыщение хромом; борирование - насыщение бором; силицирование - насыщение кремнием;
- многокомпонентные: нитроцементация (цианирование, карбонитрация) - насыщение азотом и углеродом; боро- и хромоалитирование - насыщение, бором или хромом и алюминием, соответственно; хромосилицирование – насыщение хромом и кремнием и т.д.
При тщательном соблюдении этих методов можно производить металлы различных стандартов с удивительно конкретными физическими и химическими свойствами.
Пригодность материала, используемого для детали, очень важна для того, чтобы деталь могла функционировать в предполагаемой среде. Одним из таких материалов, определяющих пригодность материала для проекта, является его твердость. Он определяет, требуется ли вашему проекту материал с высокой твердостью, например сталь, или более мягкие материалы.
Все мы знаем, что использование неправильных материалов в проекте может иметь катастрофические последствия, особенно когда произведенная деталь является частью более крупного проекта. Поэтому перед производством необходимо рассчитать предполагаемую твердость материала.
Если вам нужен материал, который может выдерживать сильное вдавливание или истирание без деформации, вам следует выбрать и обеспечить требуемую твердость материала.
Твердость материала - это способность материала противостоять силе без деформации, царапин, проникновения и вдавливаний. Другими словами, это способность материала сохранять свои физические свойства даже перед лицом приложенной силы.
Можно разделить твердость материалов на три категории. Материалы имеют разные значения для этих разных типов твердости. Они включают:
- Стойкость к царапинам
- Твердость отскока
- Твердость вдавливания
- Устойчивость к царапинам
Стандартом ГОСТ 2.310—68 (СТ СЭВ 367—76) установлены следующие правила нанесения на чертежах указаний о термической и химико-термической обработке, обеспечивающей получение необходимых свойств материала детали, должны содержать показатели свойств, которые будут получены в результате проведения необходимых технологических процессов.
- Каждый из различных типов твердости, рассмотренных ранее, имеет разные шкалы измерения :
- НВ (по Бринелю),
- HRA, HRB, HRCэ (по Роквеллу, шкала А, B, C),
- HLD, HLS, HLE (по Либу, шкала D, S, E).
- HV (по Виккерсу)
Различные типы твердости имеют разные шкалы измерения. Методы измерения твердости по царапинам, вдавливанию и отскоку различаются (например, по Бринеллю, Роквеллу, Кнупу, Леебу и Мейеру). Поскольку единицы получены на основе этих методов измерения, они не подходят для прямого сравнения. Однако вы всегда можете использовать таблицу преобразования для сравнения значений Роквелла (A,B,C), Виккерса и Бринелля. Такие таблицы не точны на 100%, но дают хорошее представление.
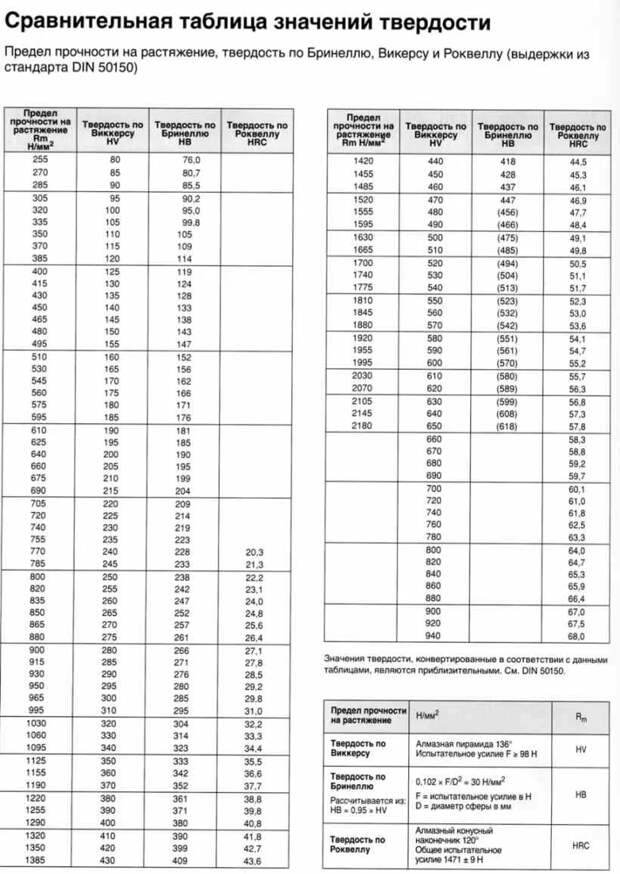
- Ударная вязкость - способность материала поглощать механическую энергию в процессе деформации и разрушения под ударной нагрузкой: ( KCV, KCU, KCT ) третий символ показывает вид надреза: острый (V), с радиусом закругления (U), трещина (Т) выражается в Дж/см2 или в кДж/м2 ;
- Предел упругости - свойство вещества, максимальное напряжение нагрузки, после снятия которой не возникает остаточных деформаций. Когда эта приложенная сила снимается, металл восстанавливает свои первоначальные размеры (если сила не превышает определенной точки). Так же, как воздушный шар, например, восстанавливает свою первоначальную форму после снятия силы после приложения: ( σу ) Н / м2 или Па ;
- Предел прочности - механическое напряжение выше которого происходит разрушение материала. Согласно ГОСТ 1497-84 «Методы испытаний на растяжение», более корректным термином является временное сопротивление разрушению: ( σв ) Н / м2 или Па.
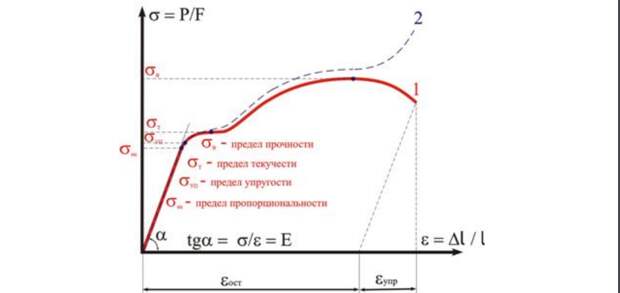
Кривая "напряжение-деформация" предоставляет инженерам-конструкторам длинный список важных параметров, необходимых для проектирования детали. График напряжение-деформация дает множество механических свойств, таких как прочность, ударная вязкость, эластичность, предел текучести, энергия деформации, упругость и удлинение при нагрузке. Независимо от того, хотите ли вы выполнить экструзию, прокатку, гибку или другие операции, значения, полученные на этом графике, помогут вам определить силы, необходимые для пластической деформации.
Наиболее распространенный метод построения кривой напряжения и деформации - это испытание стержня образца для испытаний на растяжение. Приложенная сила и возникающая деформация регистрируются до тех пор, пока не произойдет разрушение. Затем два параметра наносятся на график X-Y, чтобы получить знакомый график.
Инженер конструктор также должен учитывать соотношение механических свойств материала при создании концепции дизайна продукта. Например, при посадке подшипника и вала подшипник должен быть более мягким, потому что их легче заменить. При постоянном движении одна деталь должна изнашиваться, и выбор остается за инженером.
Учитывая специфику выбранного материала, расчеты дают ответ инженеру для необходимой площади сечения. Геометрия и термическая обработка детали играет важную роль в том, насколько высокую нагрузку может выдержать деталь. В качестве дополнительной меры предосторожности добавлен запас прочности. Коэффициент запаса прочности обычно находится в диапазоне от 1,1 до 2. При нанесении текстовой информации о величинах свойств материалов на чертеже допускается применять знаки ≤ или ≥, например: σв ≥ 1300 кгс/см2 .
Для обозначения глубины обработки на технических чертежах используется символ h .Чтобы обозначить глубину, на которую должна производиться обработка, а также необходимую твердость материала, используются предельные значения « от…до », к примеру: h0,6…0,8; 30…35 HRC.Тогда, когда это обосновано с технической точки зрения, действующие стандарты допускают обозначать эти величины их номинальными значениями с указанием предельных отклонений, к примеру: 0,8±0,1; (43±3) НRС.При нанесении текстовой информации о величинах свойств материалов на чертеже допускается применять знаки ≤ или ≥, например: σв ≥ 1300 кгс/см2 , твердость ≥ 650 HV и т.п.
Существуют разновидности термической обработки, результаты проведения которой контролю не подвергаются (таковой, к примеру, является отжиг). Кроме того, технологический процесс изготовления деталей нередко предполагает проведения только одного вида обработки, гарантирующего достижения всех требуемых свойств материала и долговечности изготавливаемой детали.
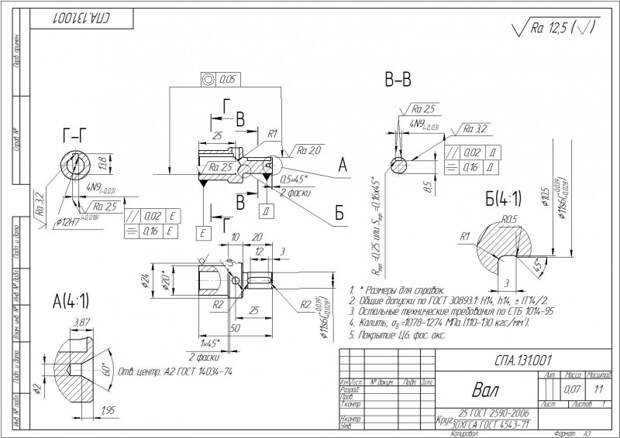
Если всю деталь подвергают термообработке одного вида, то в технических требованиях чертежа приводят требуемые показатели свойств материала; запись типа:
а) НВ235...265 или НВ250+/-15;
б) HRC44...50 или HRC47+/-3;
в) ТВЧ h1,6...2,0, HRC50...56 или ТВЧ h1,8.+/-0,2, HRC53+/-3;
г) Цементировать h 0,8...1,2 или h1,0+/-0,2 или h = 0,8...1,2; HRC56...62 или HRC5+/-3
д) Отжечь
Если термообработке подвергают отдельный участок детали, то его обводят на чертеже утолщенной штриховой пунктирной линией, а на полке линии выноски наносят показатели свойств материала. При этом используется та проекция изделия, на которой такое обозначение будет ясно определено.
Если всю деталь подвергают одному виду термообработки, а некоторые ее части другому или оставляют без обработки, в технических требованиях делают запись по типу:
а) "HRC 51..56, кроме места, обозначенного особо".
б) "HRC 65..70, кроме поверхности А".
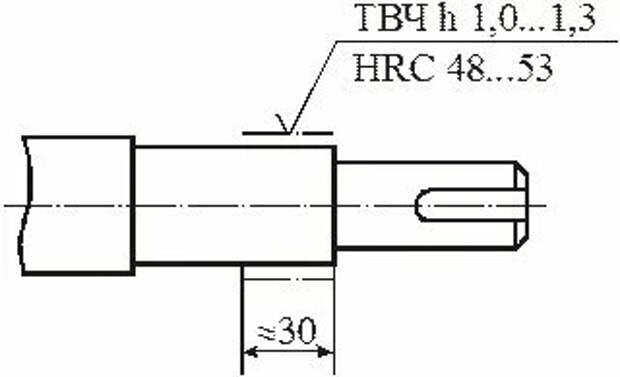
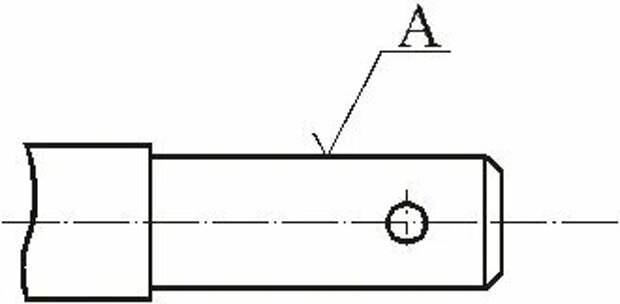
В тех случаях, когда симметричные поверхности или участки деталей обрабатываются одинаково, все они отмечаются утолщенной штрихпунктирной линией. Указание свойств материала делается только один раз.

Место испытания твердости
В случае если это необходимо, место проверки показателя твердости обозначают на чертеже в зоне требуемой твердости.
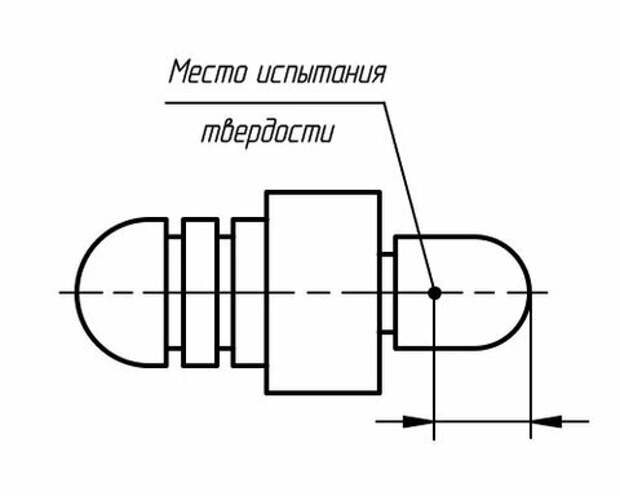
К термообработке можно привести массу положительных показателей, самыми основными преимуществами проведения подобных процессов являются:
- поверхностного упрочнения металлов и сплавов (повышения твёрдости, износостойкости, усталостной и коррозионно-усталостной прочности, сопротивления кавитации и т.д.);
- сопротивления химической и электрохимической коррозии в различных агрессивных средах при комнатной и повышенных температурах;
- придания изделиям требуемых физических свойств (электрических, магнитных, тепловых и т.д.);
- придания изделиям соответствующего декоративного вида (преимущественно с целью окрашивания изделий в различные цвета);
- облегчения технологических операций обработки металлов (давлением, резанием и др.).
Если вам сложно подобрать требуемые свойства материала и назначить термообработку, вы можете обратиться ко мне. Все, что вам нужно сделать, это отправить мне файл с вашим дизайном, и я пришлю предложение в течение 12 часов. Также предлагаю проверку возможности изготовления вашей детали / конструкции (при желании).